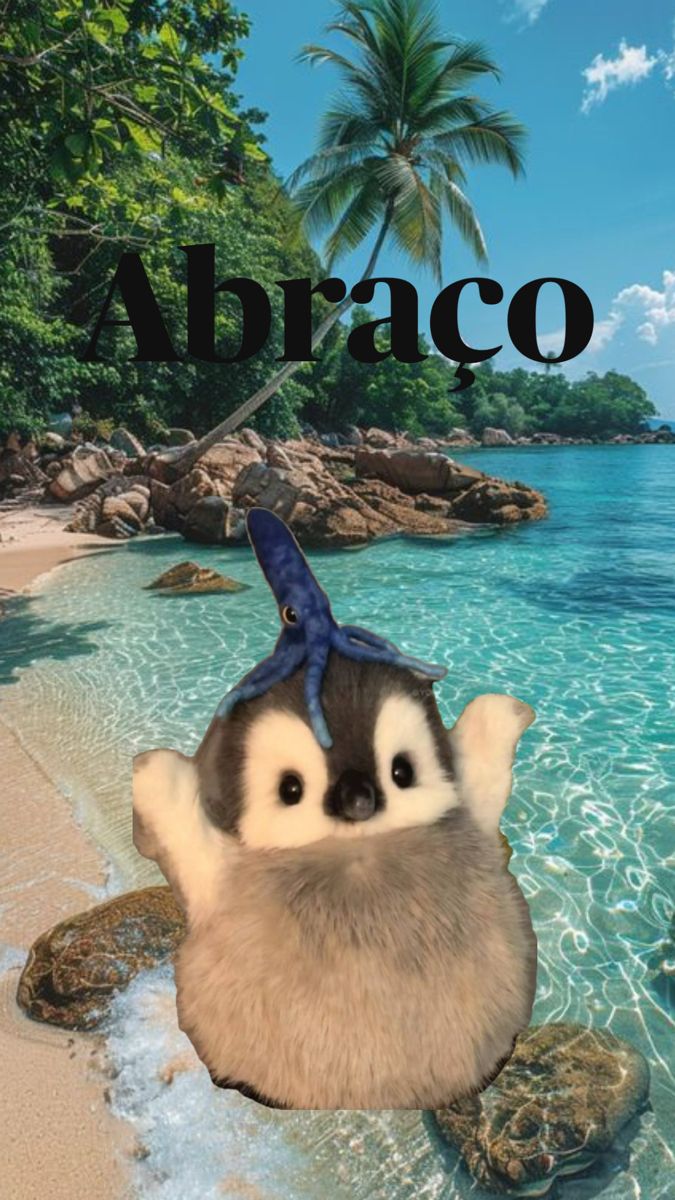
Big River Steel's Tub Seal: A Game Changer for Oil & Gas, and Beyond
Osceola, Arkansas – November 8, 2023 – Big River Steel, a leading North American flat-rolled steel producer based right here in Osceola, is making waves in a surprising new sector – oil and gas well completion. While known for high-quality steel for a wide range of industries, Big River Steel has quietly developed and is now scaling production of a revolutionary product called “Tub Seal,” a specialized sealing solution designed for oil and gas well tubing and casing. Now, you might be thinking, “Steel company making seals? What’s going on?” It's a great question. Big River Steel isn’t just throwing its hat into any ring. The company saw a real need in the oil & gas industry. Existing sealing methods often fall short, leading to costly downtime, environmental concerns, and reduced production. And let's be real, no one wants that. “We're a steel company at heart, but we’re also problem solvers,” says David Stickel, a key engineer at Big River Steel involved in the Tub Seal project. “We noticed issues with traditional sealing materials downhole. They were failing prematurely, causing leaks, and frankly, costing our customers money. We figured, we know steel, we know materials science, let's build something better.” So, what is Tub Seal? Simply put, Tub Seal isn't your grandpa’s well seal. It’s a precisely engineered, fully metallic sealing solution designed to create a reliable, permanent seal between sections of oil and gas well tubing and casing. Forget about relying on elastomers, polymers, or complicated multi-component systems. Tub Seal uses a unique, proprietary steel alloy and a clever design to literally grip and seal, creating a metal-to-metal contact that withstands extreme pressures, temperatures, and corrosive environments. Why is this a big deal? Traditional well seals rely heavily on rubber or plastic components – O-rings, packers, etc. These materials degrade over time when exposed to harsh downhole conditions – high temperatures, pressure, and the aggressive chemical makeup of oil and gas fluids. This degradation leads to leaks, requiring costly workovers to repair or replace the failed seals. Workovers are a major headache for oil and gas operators, as they involve taking the well offline, mobilizing equipment, and performing potentially dangerous repairs. Tub Seal eliminates these problems. Being fully metallic, it’s immune to the degradation issues that plague traditional seals. Here’s a breakdown of the key benefits: Permanent Seal: Once installed, Tub Seal is designed to provide a permanent, reliable seal for the life of the well. No more constant monitoring, repairs, or replacements. Extreme Durability: The proprietary steel alloy used in Tub Seal is incredibly strong and resistant to corrosion, erosion, and deformation. It can handle pressures exceeding 20,000 psi and temperatures up to 350°F – and beyond, depending on the specific alloy chosen. Reduced Downtime: By eliminating the need for frequent repairs, Tub Seal significantly reduces well downtime, maximizing production and revenue. Cost Savings: While the initial cost of Tub Seal may be slightly higher than traditional seals, the long-term cost savings are substantial. Reduced maintenance, fewer workovers, and increased production all add up. Environmental Benefits: Eliminating leaks reduces the risk of environmental contamination, protecting groundwater and surrounding ecosystems. Versatility: Tub Seal isn’t just for new well construction. It can also be used for remedial cementing, casing repairs, and even abandonment operations. How does it work? The beauty of Tub Seal lies in its simplicity. The seal features a carefully designed, multi-lobed profile that allows it to conform to minor imperfections in the tubing or casing surface. When properly installed, the lobes expand and grip the steel, creating a tight, interference fit. This metal-to-metal contact forms a barrier against fluid leakage, even under extreme pressure and temperature. The unique design also allows for some degree of axial movement, accommodating thermal expansion and contraction without compromising the seal's integrity. “We’ve spent years perfecting the geometry and the material composition,” explains Sarah Johnson, Big River Steel’s Director of Innovation. “It’s not just about making a strong seal; it’s about making a seal that stays strong for decades, even in the most challenging downhole environments.” Big River Steel: Beyond Steel Big River Steel’s foray into the sealing solutions market is a testament to the company’s commitment to innovation and its ability to adapt to changing market needs. The company isn't just a steel supplier; it's a materials science leader, constantly exploring new applications for its products and technologies. “We’re proud to be a Made in America company, creating high-quality products and supporting local jobs,” says Rick Stone, CEO of Big River Steel. “Tub Seal is a perfect example of how we’re pushing the boundaries of what’s possible, delivering innovative solutions that benefit our customers and the environment.” Looking Ahead Big River Steel is currently ramping up production of Tub Seal to meet growing demand. The company is also working on developing new seal designs and alloys to address even more challenging downhole conditions. “We see a huge potential for Tub Seal to become the industry standard for well sealing,” says David Stickel. “We’re confident that our product will save our customers money, reduce downtime, and help them operate their wells more safely and efficiently.” For more information on Tub Seal, or to request a quote, please contact Big River Steel at 816-810-1342 or visit their website at [Insert Website Address Here - Not Provided].